Courses
Manufacturing Management
Bachelor of Engineering
Course Details
Course Code | SG_EMANM_J07 |
---|---|
Level | 7 |
Duration | 2 years |
Credits | 60 |
Method of Delivery | Online |
Campus Locations | Sligo |
Mode of Delivery | Part Time |
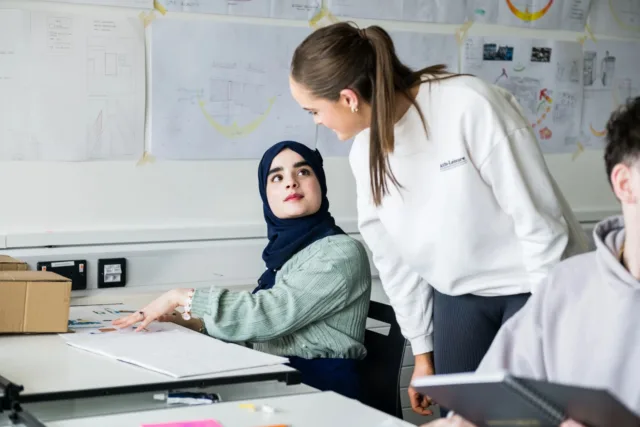
Course Overview
This course is aimed at those currently working, or aspiring to work in management or supervisory positions in a manufacturing or service organisation. Graduates from this programme hold front-line management positions with leading multinational and SME employers across Ireland. The course teaches key skills that front-line managers need to learn to grow and adapt to changing work environments in modern organisations.
Topics covered include Lean Six Sigma, Quality Management Systems, Project Management, Lean Management Techniques, Occupational Safety & Health, Statistical Control, Production Management, People Management, Managing Accounting and professional development.
Students completing the BSc Manufacturing Management degree also meet the requirements of the internationally recognised Six Sigma Green Belt award. Students may receive this award in addition to their degree by sitting an external Green Belt exam.
About this Programme
This degree offered via online distance learning aims to deliver a broadly based degree with lecturers from the schools of Engineering and Business and Humanities at ATU Sligo. The Lean Six Sigma element to the programme which is covered exclusively in three of the twelve modules, is an element many participants finds very beneficial in their work environments.
This course is aimed at those currently working, or aspiring to work in management or supervisory positions in a manufacturing or service organisation. Graduates from this programme hold front-line management positions with leading multinational and SME employers across Ireland. The course teaches key skills that front-line managers need to learn to grow and adapt to changing work environments in modern organisations. Topics covered include Lean Six Sigma, Quality Management Systems, Project Management, Lean Management Techniques, Occupational Safety & Health, Statistical Control, Production Management, People Management, Managing Accounting and professional development.
Course Details
Year 1
Semester | Module Details | Credits | Mandatory / Elective |
---|---|---|---|
Year |
People Management in PracticeThis module aims to introduce the learner to a range of human resource management issues from the perspective of a line manager and in the context of ensuring compliance to relevant legislation. Learning Outcomes 1. Appreciate the psychological contract of employment. 4. Facilitate a disciplinary meeting. |
05 | Mandatory |
Year |
Production ManagementThis module provides a foundation to Production Management concepts and techniques. The historical development of production up to today's modern environment are addressed. Product and Process Design, Layout Planning and Forecasting are introduced. Capacity and Inventory Planning, Materials Planning and Scheduling are explained. Learning Outcomes 1. Explain the development of modern production management 3. Explain how customers needs are transferred into product specification 4. Compare the different types of production systems 6. Display an understanding of capacity planning, inventory policies, materials planning and scheduling |
05 | Mandatory |
Year |
Project ManagementThe student should be able lead a small project team or to provide technical and local support to a Project Manager on a large distributed project. Learning Outcomes 1. Discuss the project environment, characteristics, objectives, life cycle phases and the dimensions of project success |
05 | Mandatory |
Year |
Organisational BehaviourThis subject aims to provide the students with an understanding of the basic principles underlying workplace behaviour and to increase their ability to analyse issues that concern individuals and groups in organisations. Learning Outcomes 1. Analyse the methodologies used in organisational behaviour research. 3. Apply the principles of learning to various organisational activities. |
05 | Mandatory |
Year |
Quality Management SystemsQuality Management Systems is intended for anyone working in any manufacturing or service sector where a structured approach to product/service quality and customer satisfaction is important. It is ideally suited for those who have some experience of work life at any level and who now wish to develop a deeper understanding of the standards and approaches that facilitate and maintain quality at process and organisational level. The primary emphasis of the course is on the the ISO9000 family of Quality Management System standards but it also looks at equivalent standards in the automotive, pharmaceutical, medical device and food sectors. Related systems such as Environmental and Health and Safety get a mention in terms of similarity and opportunities for integration. Learning Outcomes 1. Interpret the requirements of the various standards in the ISO9000 family of quality management system standards. 4. Plan and conduct audits. |
05 | Mandatory |
Year |
Management AccountingThe aim of this subject is for the student to have developed a good understanding of the nature of accounting for decision making and an ability to interpret such information and apply it to particular problems and situations within an organisation. Learning Outcomes 1. Describe the nature and purpose of management accounting. |
05 | Mandatory |
Year |
Professional Development SkillsThis module aims to further develop the learner's interpersonal communication and managerial skills in the context of professional work practice. Learners will participate in reflective activities that will facilitate the development and practice of professional business skills. Learning Outcomes 1. Identify communication strategies that illustrate personal effectiveness. |
05 | Mandatory |
Year |
Six Sigma 2 Statistical ControlThis module aims to provide learners with the statistical tools associated with the six sigma DMAIC philosophy specifically in the areas of Measure, Improve and control consistent with the ASQ and Quality America Green Belt Body of Knowledge. The student will be able to perform basic statistical analysis, develop and plots control charts, determine process and measurement capability. Minitab statistical software will be used to demonstrate and apply these statistical techniques. Learning Outcomes 1. Perform basic probability calculations by applying the probability rules and concepts |
05 | Mandatory |
Year |
Lean Management TechniquesThis module aims to give the student the necessary skills to apply Lean tools and techniques in a workplace environment . The history and developmnent Lean and the Lean Philosophy is introduced. The Lean Principles and Lean Transformation Frameworks are identified.. The tools and techniques such as value stream mapping, standardisation of work, error proofing, visual signals and pull systems used to identify and eliminate waste (non-value added activities) through the entire process. Learning Outcomes 1. Describe the benefits of applying \”Lean Management\” techniques in a manufacturing or service environment 3. Describe a Lean Transformation Framework |
05 | Mandatory |
Year |
Project Six Sigma 3The project aims to provide students with the opportunity to apply and integrate the skills and knowledge they have gained on the programme. For students in employment, the project should address a substantive issue in the workplace. The project will test the student’s ability to define a real-life problem of concern to the organisation, design a strategy for addressing the problem, gather data, formulate and evaluate options and make recommendations. The project must follow the DMAIC problem-solving methodology using Lean and/or Six Sigma tools. For students not in employment and unable to complete a work-based project, then a simulated Lean Six Sigma project option may be undertaken. This will consist of reviewing six sigma case studies, analysing the data and using the appropriate Six Sigma tools and Minitab statistical software to identify the solutions to the problem. A mentor will be assigned to each project, which may be individual or in some cases group projects. The mentor will act as a guide in agreeing the relevance, and scope of the project and monitor the progress on a regular basis. There will be regular contact between the student and their mentor as the project progresses throughout the semester. Updates will be sent to the mentor on an agreed basis. Learning Outcomes 1. Identify a problem which needs to be addressed of importance to the organisation. 4. Present project results with Executive Summary, Conclusions and Recommendations and justify the approach that was taken and the results achieved. |
05 | Mandatory |
Year |
Six Sigma 1 – Introduction to Lean Sigma QualitySix Sigma 1 ‑ Introduction to Lean Sigma quality aims to provide learners with an understanding of the tools and techniques of quality that are used in the attainment of a six-sigma quality environment. The principal goal of Six Sigma is to reduce variation in the process and improve quality. Through practical examples and exercises, learners will become proficient in the use of the basic problem-solving techniques used to monitor and control processes. The topics include: the Six Sigma DMAIC problem-solving process, Lean principles, FMEA's and risk management, the seven traditional quality tools, surveys, descriptive statistics and an introduction to inferential statistics. The module now includes lectures on Minitab – the industry-leading Six Sigma statistical software. This module is also designed to meet the requirements of the Six Sigma Yellow belt award. This module aligns with the internationally recognised Six Sigma Green Belt body of knowledge from the American Society for Quality (ASQ) and also from Quality America. As this is an online course, the majority of students are working in industry. Learning Outcomes 1. Describe why organisations use Six Sigma andthe Design for Six Sigma (DFSS) and DMAIC improvement methodology. 6. Calculate process performance metrics such as DPU, FTY, DPMO and Cost of Poor Quality (COPQ). |
05 | Mandatory |
Year |
Occup Safety and HealthThis module will give students a foundation in occupational safety and health and highlight the links between environmental issues and health and safety in the workplace. Learning Outcomes 1. Identify a variety of hazards in the workplace and apply appropriate control measures 2. Outline the parameters used for Occupational Safety andHealth monitoring in Ireland 3. ExamineOccupational Safety and Healthlegislation in Ireland andidentify the roles of the various stakeholders involved including employers and employees 4. Communicate the need for effective management of Occupational Safety andHealth issuesin the workplace 5. Examine the links between environmental issuesandoccupational safety andhealthissues in the workplace. |
05 | Mandatory |
Recommended Study Hours per week
Examination and Assessment
Note: Where assessment on the programme involves examinations, these are held on campus or at another exam venue in the Republic of Ireland. There are typically two exam periods: January and May. Times scheduled for examinations (face to face / online exams ) are in GMT.
Students who are resident overseas and those with extenuating circumstances may apply to take examinations online with an external online invigilation service (online proctored exams), where this is available. Places are limited for this service.
On-Campus Attendance Requirement
Note: Check programme Examination and Assessment requirements, as they may involve examinations to be taken on campus.
Download a prospectus
Entry Requirements
The BSc Manufacturing Management is the final year of a Level 7 degree course offered over 2 years part-time. Applicants will be expected to hold a Level 6 National / Higher Certificate in Business, Science, Engineering or equivalent. Applicants with other qualifications and/or with relevant experience may also be considered through ATU Sligo’s Recognition of Prior Learning (RPL) process.
If you wish to undertake an online Level 6 course at ATU Sligo, a suitable course would be as follows: Level 6 Certificate in Quality Assurance (30 credits) Level 6 Cert in Validation Technologies (30 credits) Level 6 Work-Based Project (30 Credits) You can complete any two of the above programmes over 1 year to obtain 60 credits at Level 6. These 60 credits combined with suitable work experience would allow you to apply for entry onto the Level 7 BSc Manufacturing Management degree via our RPL process. If you do not meet the normal eligibility requirements or you have qualifications from outside Ireland, please email admissions.sligo@atu.ie who will provide you with further guidance on the entry requirements.
Careers
A graduate from this programme will have the necessary technical and business skills to manage a group of employees in a modern manufacturing environment. By combining operations and project management with quality, health & safety, finance and leadership skills, the graduate is ideally equipped to take up positions as a team leader or front-line manager in a manufacturing or service environment.
Graduates of this course are employed in the following roles:
• Production Supervisor
• Line Facilitator
• Team Leader
• Production/Shift Manager
• Operations Manager
• Manufacturing Manager
• Factory Supervisor
• Warehouse Shift Lead
•Production Line Manager
Further Information
Who Should Apply?
This course is aimed at those currently working, or aspiring to work in management or supervisory positions in a manufacturing or service organisation. Graduates from this programme hold front-line management positions with leading multinational and SME employers across Ireland.
Application Closing Date
Start Date
Contact Information
Online Student Advisor
Kevin Colonna
T: +353 (0) 71 930 5219
E: Kevin.Colonna@atu.ie
Mechanical & Manufacturing Engineering