View all Courses
Breakthrough research by ATU into skin care unveils revolutionary technology for pharmaceutical industries using artificial intelligence
Breakthrough research by ATU into skin care unveils revolutionary technology for pharmaceutical industries using artificial intelligence
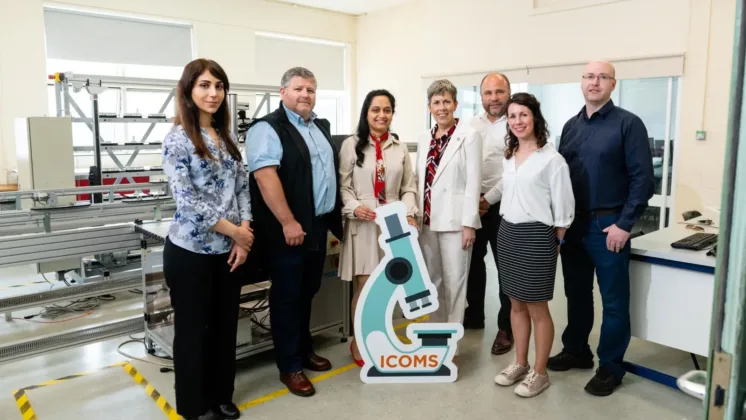
The skin care industry is estimated to have a value of over €130 billion globally and is predicted to grow by 4% year on year to 2030.
Whether the product is for personal skin care, medications, or cosmetics producers of skin care products face the same challenge, namely the stability of the product. For example, “Are you familiar with precipitated pigments in a skincare lotion and/or suspended particles swimming on top of or settled at the bottom of a moisturiser bottle?” these undesirable characteristics are a result of the instability of the product. Improving the stability of the final product, which most commonly are emulsions (a product consisting of tiny droplets of one liquid dispersed within the other) requires detailed information about the emulsion structure, achieved through microscope analysis.
Industries grappling with highly concentrated pharmaceutical emulsions (phase fraction > 0.5) face increasingly complex challenges in achieving real-time characterisation and producing a stable formulation. However, a ground-breaking research study led by a research team at Atlantic Technological University has revealed a patented technology that combines microscopic image-based analytics with artificial intelligence algorithms, offering a transformative solution to this intricate problem.
The research, now funded by Enterprise Ireland for commercialisation, has demonstrated the potential of this innovative approach in simplifying, streamlining, and making emulsion manufacturing more efficient and sustainable. The technology, known as ICOMS (Inline Characterisation of Multiphase Systems), conducts automated feature extraction on micrograph samples to analyse emulsion droplet size/shape characteristics and predict in-process product quality using Machine Learning techniques.
One of the key highlights of the research is the exceptional recognition ability achieved by the ICOMS technology. When used to analyse the Droplet Size Distribution (DSD) of oil droplets in topical skin care emulsions, the technique showcased a recognition ability as high as 99%. This remarkable result underscores the significant potential of ICOMS in reducing over-processing and optimising the manufacturing of emulsion products.
Conventional methods of quality analysis for pharmaceutical emulsions have long been deemed subjective and time-consuming, leading to inefficiencies and potential inaccuracies in production. However, the ICOMS approach presents impressive advantages over traditional methods.
Key Highlights of the Research:
Unprecedented Speed and Accuracy: In comparison to conventional approaches, the innovative technique proved to be 180 times faster while achieving an accuracy improvement of up to 40%. This substantial increase in efficiency enables manufacturers to optimise their processes and achieve superior quality control standards.
Automation for Enhanced Sustainability: The automated approach demonstrated promising potential in reducing the over-processing of pharmaceutical emulsions. By saving approximately 8% of the processing time for every batch, this technology may have the capability to significantly minimise resource wastage, decrease energy usage, and substantially reduce production costs in some cases by an estimated 93%. Embracing such sustainable practices is vital for the future of the industry.
President of ATU, Dr Orla Flynn said the research opens opportunities for industries; “Given my own tech background I found this project really interesting, with the opportunities it opens up for industries to embrace the recent advances in disruptive technologies such as computer vision and artificial intelligence to achieve their sustainable manufacturing goals.”
Dr Saritha Unnikrishnan, the lead principal investigator of ICOMS at Atlantic Technological University, expressed her enthusiasm about the results, stating; “Our technology represents a major milestone in the field of emulsion droplet morphology analysis. The technology is at a readiness level of TRL-6, which is undergoing further research to commercialize it as an intelligent soft sensor. The ICOMS system, with its automated microscopic image-based analytics and artificial intelligence algorithms, opens up new possibilities for efficient resource utilisation, and reliable, and sustainable emulsion manufacturing, thereby optimizing economic feasibility and reducing environmental impact. We are thrilled to be at the forefront of this ground-breaking innovation.”
This collaborative research project, led by Dr Saritha Unnikrishnan, Dr Marion McAfee, Dr Xavier Velay, and Finola Howe, along with the newly recruited project team consisting of Dr Alan Hernon as the business lead, Hanieh Khosravi as the Computer Vision Engineer, and Ross McMorrow as a full-stack MLOps developer, showcases a diverse expert team and the university’s commitment to advancing scientific excellence towards driving innovation. The background of this research originated from the Ph.D. research carried out by Dr Saritha Unnikrishnan with the supervision of Dr David Tormey, Dr John Donovan, and Dr Russell Macpherson.
As part of the commercialisation project (202325), the team aims to further develop the patent-published (US20210354096A1) emulsion analysis technology and establish a new spin-out company to bring it to market. The team has plans to extend the approach from pharmaceuticals to food, dairy, and biofuel industries. This endeavor will focus on creating novel offline (and potentially inline) soft sensor systems for characterising emulsion product quality and stability.
Dr Unnikrishnan added; “Atlantic Technological University, is excited to collaborate with pharmaceutical companies and other industries dealing with highly concentrated emulsions. Together, we can harness the power of the ICOMS technology and leverage its potential to optimise production, reduce costs, and elevate quality standards.”